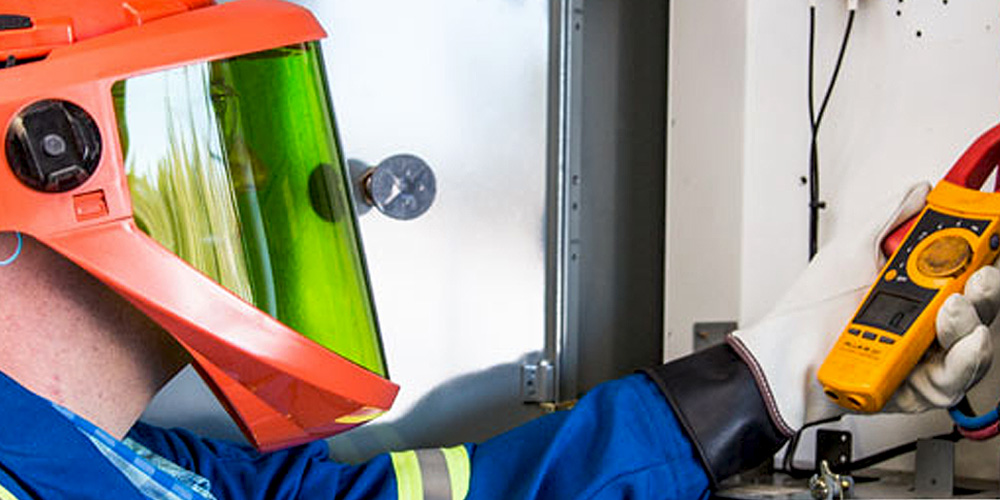
Health, Safety, Environment
Learn more about our robust safety management system that is an integral part of our company that helps protect our staff, clients and the environment.
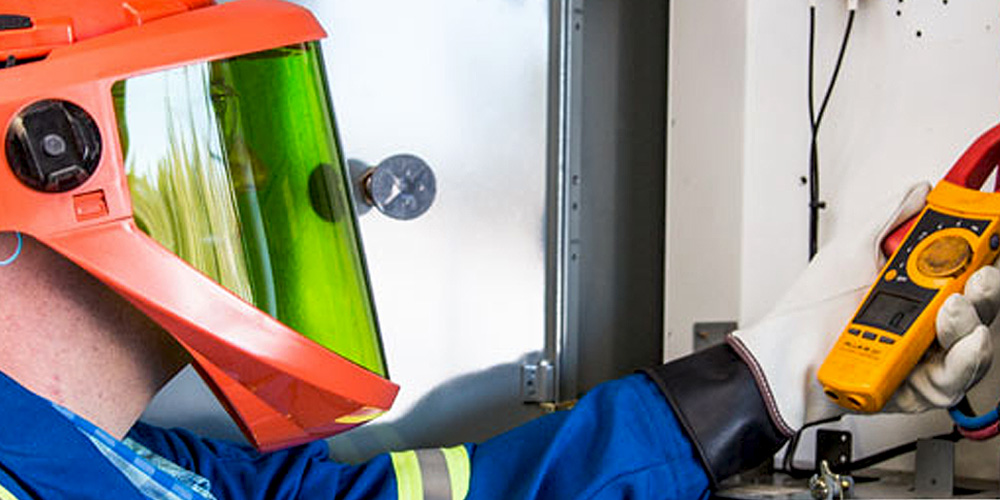
Health, Safety & Environment
Learn more about our robust safety management system that is an integral part of our company that helps protect our staff, clients and the environment.
HSE Goal
HSE Goal
At CFI, the health and safety of everyone at our worksites is a key component of how we do business everyday. This commitment to providing quality workmanship done in a safe manner, ensures that everyone can work without fear of injury or harm and we are committed to implementation of robust safety management systems, comprehensive training and fostering a culture of safety awareness and continual improvement.
Environmental Commitment
Environmental Commitment
CFI is committed to protecting the environment, ensuring a safe workplace, and adhering to all applicable environmental and health regulations all while promoting sustainable practices.
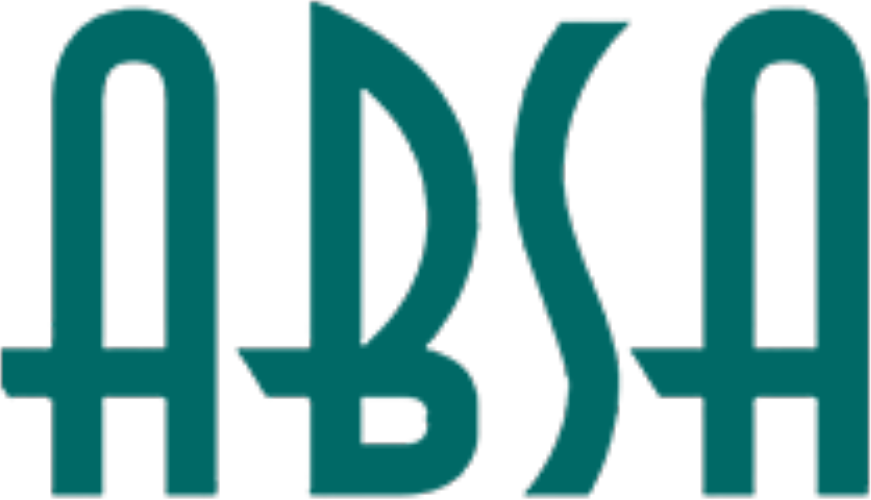
CFI is certified by ABSA, the pressure equipment safety authority in Alberta, and has developed a Quality Management System (QMS) to meet ABSA’s requirements for safe construction, installation, repair and alteration of instrumentation tubing and non-welded pressure piping. The QMS accurately describes the systems to be used by CFI when working with tubing or piping, in compliance with company policies, owner’s requirements, ASME B31.1 or B31.3 Process Pressure Piping Codes, and the Alberta Safety Codes Act of Alberta.
Workplace Health & Safety
Strong leadership at all levels at CFI is an integral part of the proactive approach towards protecting our people, our client companies, stakeholders, and the public. Our comprehensive safety management system ensures our employees, contractors and visitors are involved and proficient in hazard and risk assessments, inspections, audited activities, training, and competency evaluations to ensure the health and safety of our worksites.
Key Areas Of HSE at CFI:
- Management Commitment – A strong leadership group with extensive trade knowledge and commitment to ensuring work is done in with quality and health and safety at the forefront.
- Strong Hazard Assessments – The cornerstone of health and safety, the management of risk begins with hazard assessment and requires trained and competent workers to implement controls to minimize risk.
- Continuing Improvement – Safety management systems require inspections, audits, training, emergency preparedness as well as care and attention to detail to ensure that our workforce has the knowledge and resources to move our program forward while promoting a strong safety culture for all.
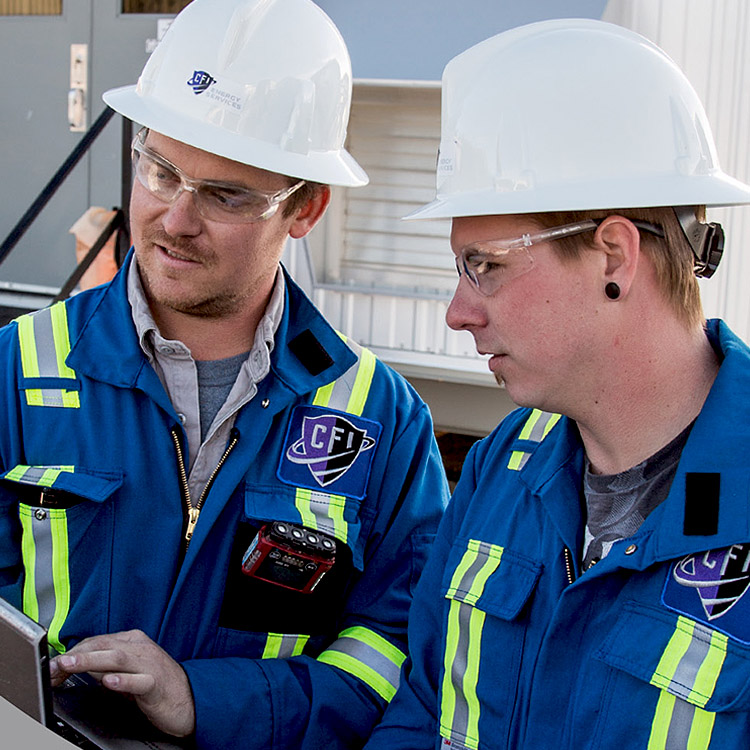
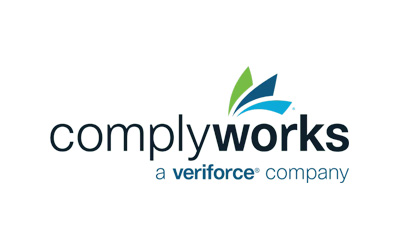
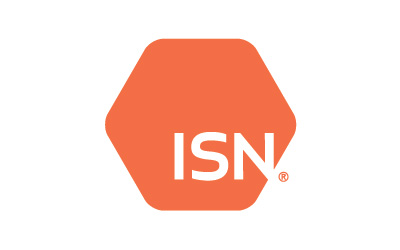
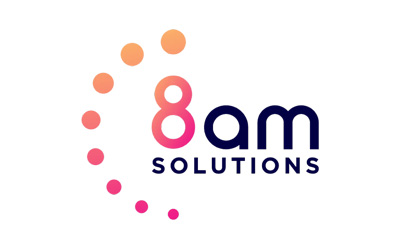
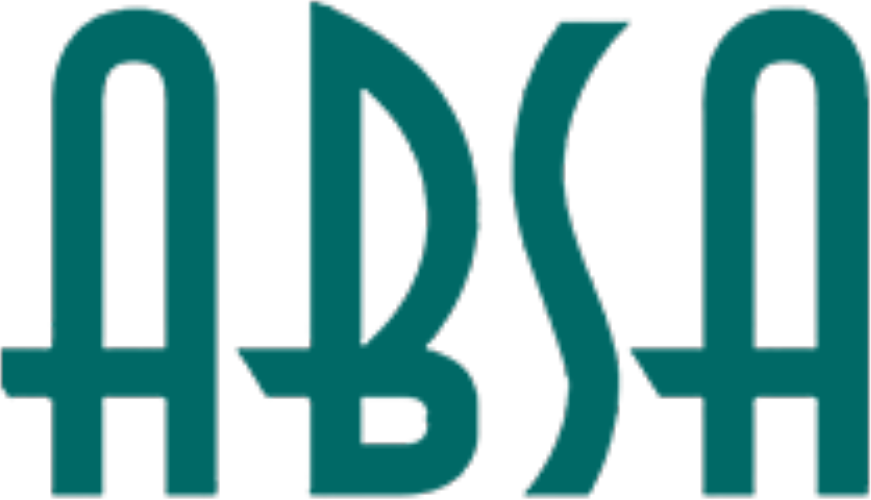
CFI is certified by ABSA, the pressure equipment safety authority in Alberta, and has developed a Quality Management System (QMS) to meet ABSA’s requirements for safe construction, installation, repair and alteration of instrumentation tubing and non-welded pressure piping. The QMS accurately describes the systems to be used by CFI when working with tubing or piping, in compliance with company policies, owner’s requirements, ASME B31.1 or B31.3 Process Pressure Piping Codes, and the Alberta Safety Codes Act of Alberta.
Workplace Health & Safety
Strong leadership at all levels at CFI is an integral part of the proactive approach towards protecting our people, our client companies, stakeholders, and the public. A comprehensive safety management system ensures our employees, contractors and visitors are involved and proficient in hazard and risk assessments, inspections, audited activities, training, and competency evaluations to ensure the health and safety of our worksites.
Key Areas Of HSE at CFI:
- Management Commitment – A strong leadership group with extensive trade knowledge and commitment to ensuring work is done in with quality and health and safety at the forefront.
- Strong Hazard Assessments – The cornerstone of health and safety, the management of risk begins with hazard assessment and requires trained and competent workers to implement controls to minimize risk.
- Continuing Improvement – Safety management systems require inspections, audits, training, emergency preparedness as well as care and attention to detail to ensure that our workforce has the knowledge and resources to move our program forward while promoting a strong safety culture for all.
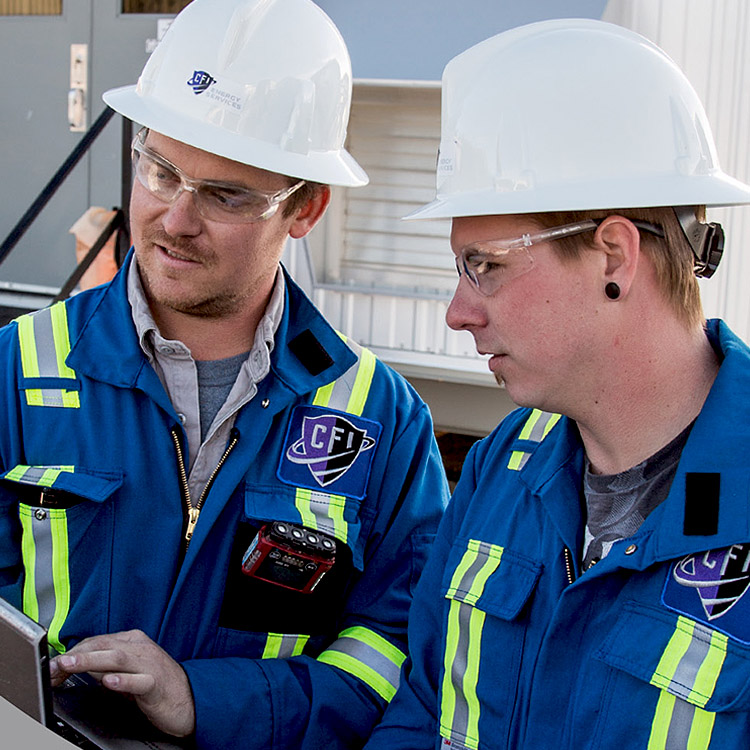
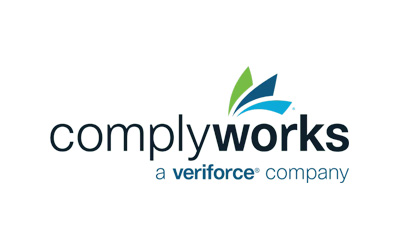
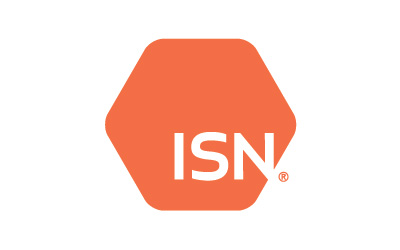
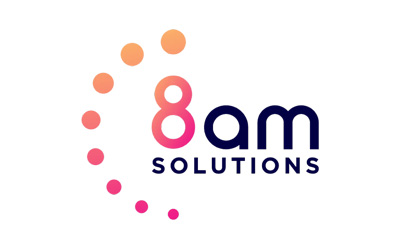